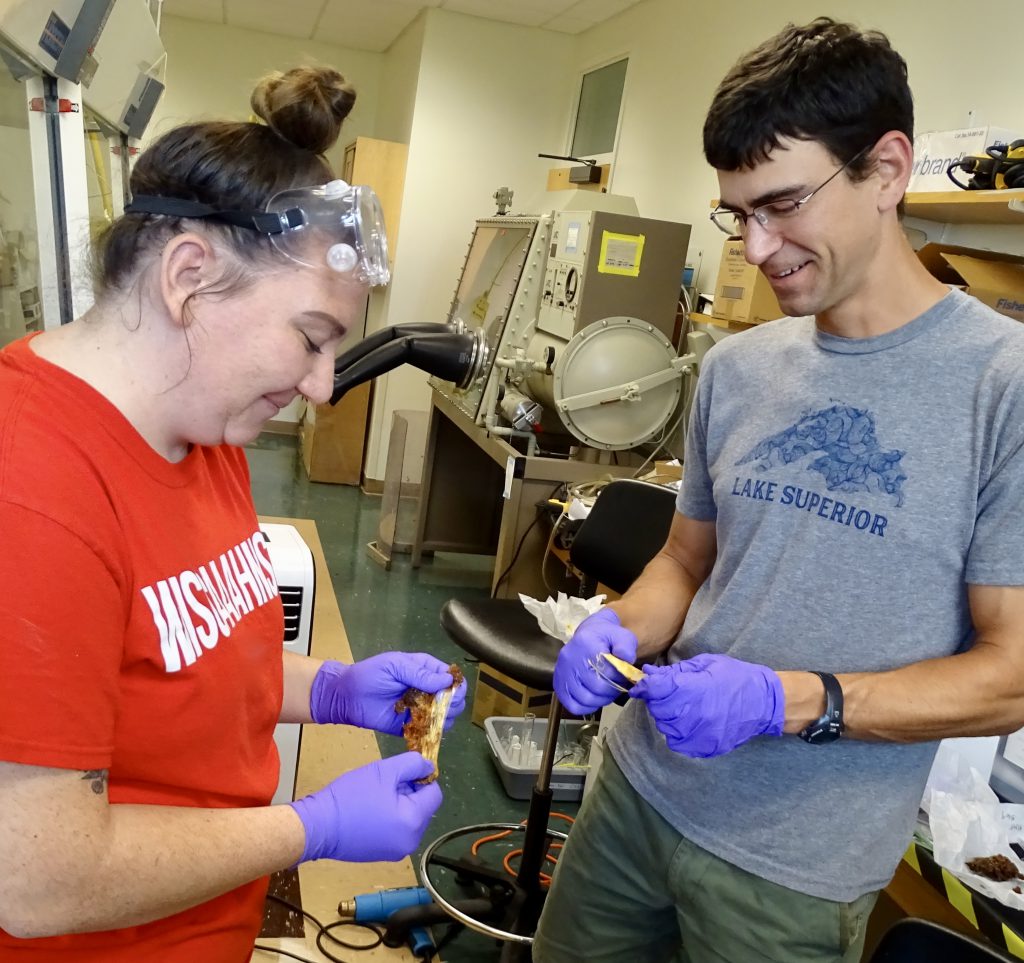
The activities are as follows:
Plastics are materials that can be shaped easily and are used for many functions. This has made them extremely popular across the world. Thousands of products are made using plastic, including parts of cell phones, food wrappers from your lunch, and even the stitches you may need after an injury. In fact, if you look around right now, you can probably spot at least ten items made of plastic!
Once a plastic is made, it tends to stick around. Synthetic plastics, made by humans from petroleum, cannot be broken down by nature’s decomposers – bacteria and fungi. This means they impact the environment for many, many years. Some types can take thousands of years or longer to break down!
Nick is a chemist concerned with the negative impacts caused by plastics. He knows that in order to reduce the amount of synthetic plastics in the environment, we need an alternative. And, this alternative needs to be just as good as the synthetic plastic it is replacing. Nick and his undergraduate students at Northland College are testing new ways to make plastics that are biodegradable, meaning they can be decomposed naturally and won’t last as long in the environment. His research focuses on stretchy plastics, called elastomers.Elastomers are what make up rubber bands, tires, hoses, non-latex gloves, and many more items we use every day.
To try to solve the problem of making a biodegradable elastomer that has all the qualities of a synthetic one, Nick and his students got to work. First, they had to consider the chemical structure of plastics. Plastics are made of polymers. “Poly” means “many” and “mer” means “parts”. This means that plastics are made of long chain molecules with many repeating parts. These repeating parts are called monomers. Different monomers can be used to make different types of plastic.
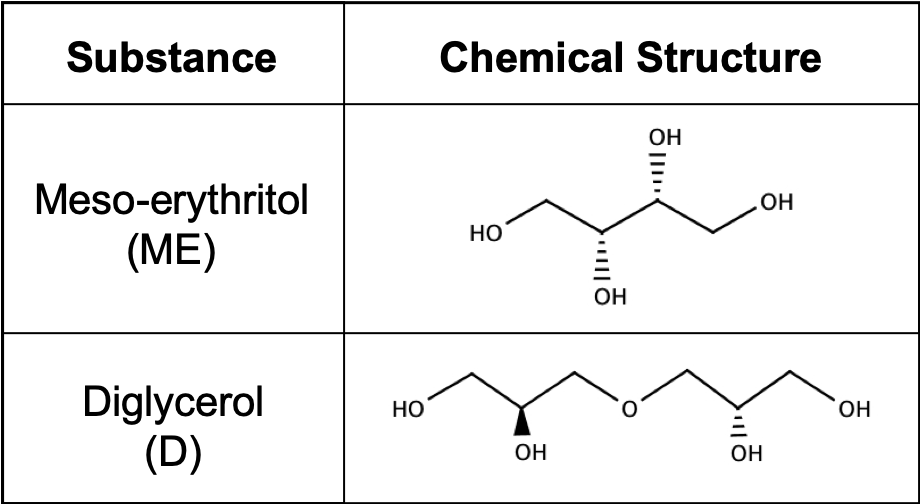
Nick chose to test two biodegradable monomers – diglycerol and meso-erythritol. Diglycerol is cheap and easy to buy. However, it might be too soft when used on its own. Meso-erythritol is more expensive, but more rigid. They wanted to use diglycerol and meso-erythritol because the chemical structures have the potential to create something that is not too rigid and not too flexible.
Nick and his students designed an experiment in which they tested elastomers made from each of the monomers (diglycerol and meso-erythritol) alone, as well as elastomers made using both types of monomers. They made elastomers with the following percentage ratios of diglycerol over meso-erythritol: 100/0, 75/25, 50/50, 25/75, 0/100. The team was hoping to find the “sweet spot” between a product that is too stiff, and one that is not stiff enough to be useful in elastic materials. Once they finished making their elastomers, they prepared the stretch tests.
To start a stretch test, the team had to stamp out a piece of material from each elastomer, creating samples with the same size, shape, and thickness. They also cut pieces from rubber bands made of synthetic plastics to compare as a control. Next, they tested the elastomers using a machine that measures how much force is applied (stress) as a material is stretched (strain), both important measures of elasticity. The stress, or force per unit of area, is measured in megapascals (MPa) while the strain, or amount of stretch, is measured as a percent of the original length.
Featured scientist: Nick Robertson from Northland College. Written by: Theresa Paulsen from Ashland High School, Wisconsin
Flesch–Kincaid Reading Grade Level = 9.6
For additional information on the plastic problem, and Nick’s research, check out the following resources:
- Plastics Resources – National Geographic
- We Need to Rethink Plastics – interview with Nick Robertson
- Functional Groups in Organic Molecules – video lesson